01
走进现场
什么是“走入现场”的真正含义呢?许多人都自认为了解“现场”,因为他们就是在现场工作。
但是亲身出现在现场,与了解现场是两件不同的事。
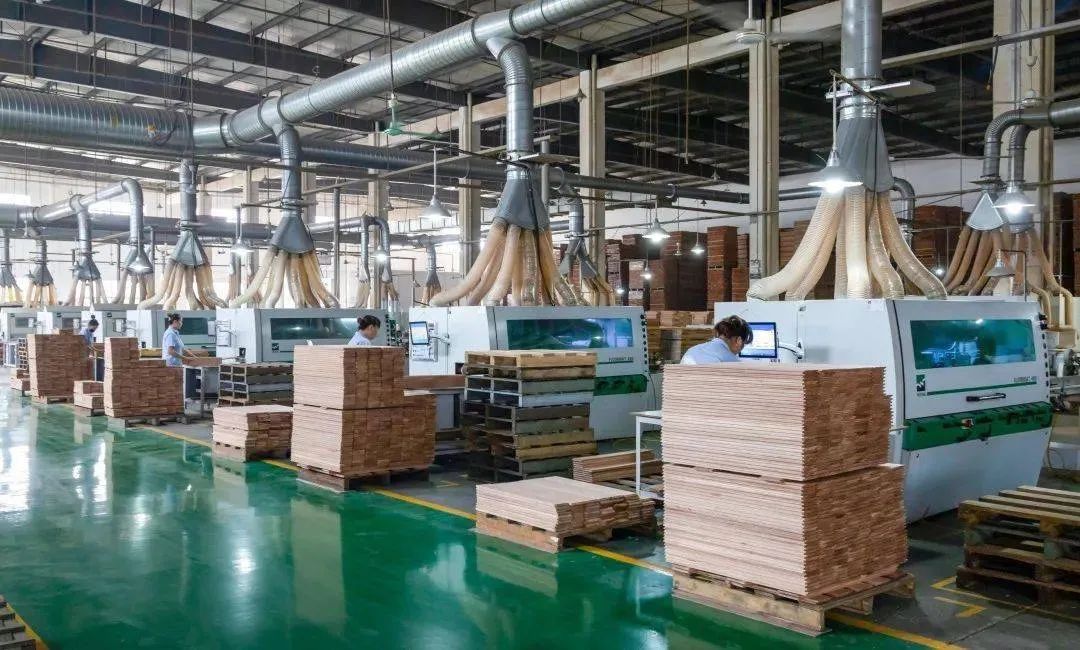
《生产线改善》的作者高桥昭雄说:“只是单纯地走到现场去东看看、西看看是不够的。真正的了解现场,是指自己能够以明确的名词和数值,来表达所看到的现场现象。”
在生产线上说:“这工厂管理得不够好!”是没有什么意义的。
管理人员应当说:“A生产线的可动率是65%,但是应该可以提升到85%。”
我们应当使用特定的名词和数值来表达,使我们在讨论的时候,有共同的基准,这些都会使问题更容易解决。
现场改善,指要走入现场,去观察、发掘。并能当场即时解决任何问题。
日本的制造厂商,多擅长在买卖双方达成共识的条件下,以合理的价格供应优质的产品和服务。
这种具有高度成效的生产体系,是由现场改善实践和过去50年来,持续不断的改善所贡献出来的。
02
发掘现场问题
开始之前,管理人员要先具备了解现场改善的基本知识,例如:浪费,厂房环境维持、可视管理及标准化。
通过自主研究会改善活动,可以减少某一流程的作业人数、降低库存量和缩短交期时间。
03
两天期改善
两天的现场改善,是以目标设定明确化开始。例如:一位厂长预期下个月的需求量。会提高20%的生产量。他与生产线经理讨论之后,同意在A生产线做为期两天的现场改善活动。
这是瓶颈作业的所在。
通过生产线布置和改善,来作为达到这一目标的手段。
方式:选定某一生产线为改善对象,并要求在两天以内完成。
时间:利用生产线下班后晚上的时间,不干扰正常的生产活动。
参与人员:通常包括了工厂内的主要人物,例如:厂长、生产线经理、督导人员、领班和作业人员。
流程:
第一天:
维修人员和改善工厂线路的工人要随时待命。
研讨会在下午六点结束。
新的改善方案要即刻实施。
安装好各项器具,改善小组和课长即刻启动生产线试做,以确保能正常运行。
第二天:
比平时早半个小时上班。改善小组向作业员解说生产线的改变和新的工作程序。
生产作业和平时一样,在八点钟开始。
改善小组的组员一直待到上午十点,让作业人员有时间习惯新的流程。
改善小组组员则在此期间内,将所遇到的问题做成一览表。
任何必要的修正事项一经完成之后,作业人员立刻就在线上进行操作,小组观察并测量结果。
小组在下午四点之前,将两天活动的总结准备完成,四点钟则开始作结案发表会。
在发表会之后,仍有许多事要跟催执行,例如:成果确认、工作标准的修订;有时,还有工程规范和标准的修订。
04
六项标准
001设立一条能依据产距时间生产的生产线。
002设立一条能随产距时间变化且有弹性能力的生产线。
003彻底的消除作业中的无序、浪费和混乱。
004排除阻碍生产顺畅和谐的因素。
005开发标准化流程。
006生产线尽量机械化。
05
改善工具
列出各项清单,对照清单来进行调整变化。
例如:“动作经济原则”的检查表
A.消除不必要的动作
1.剔除寻找或选择某些东西的动作
2.剔除需要作判断或特别注意的动作
3.剔除工作中两只手之间的转化动作
B.减少眼球动作
1.用听觉代替视觉
2.用灯号
3.把所有要用到的物件,都放在相关作业人员的视线内